BioCompatic: a great solution for medical cables
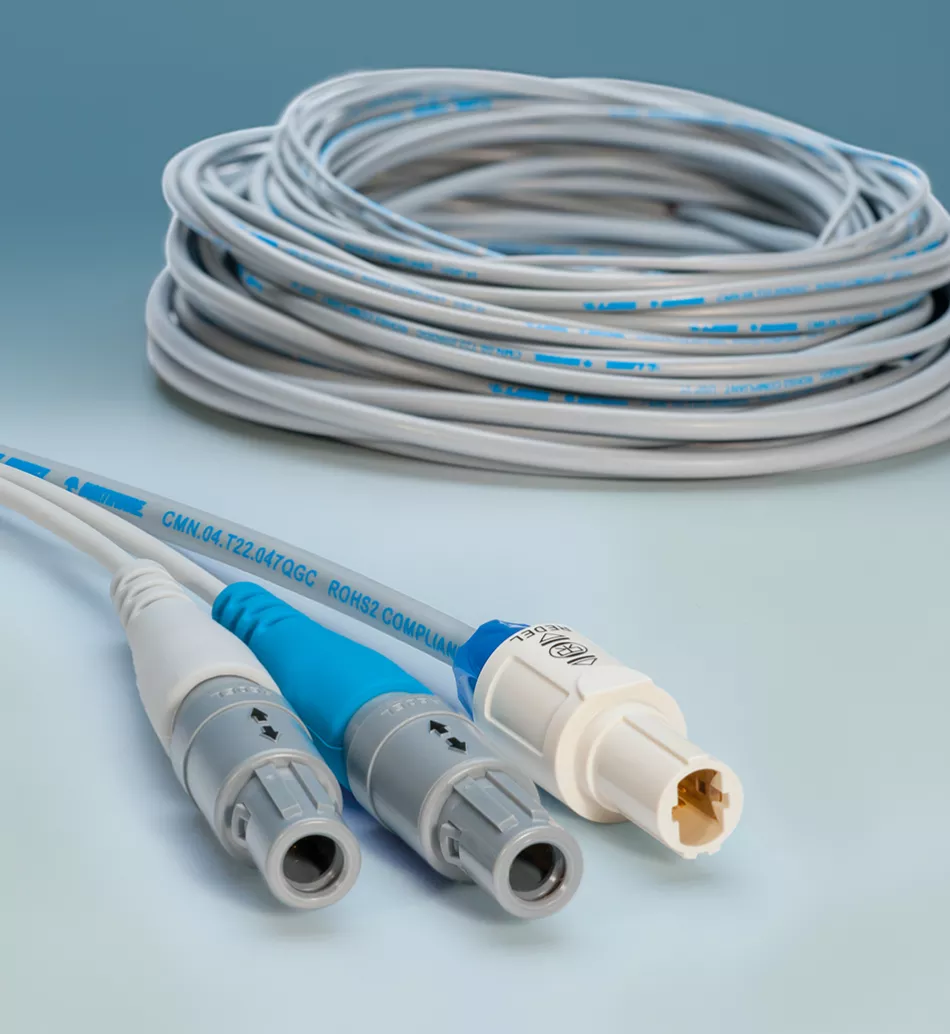
Northwire has just launched a brand new cable with unprecedented specifications. Flexible, resilient, supple and biocompatible, it is a great alternative to silicone cables. This is a small revolution in the medical sector which could also be interesting for other demanding environments.
Until now, silicone was the undisputed leader among cable jackets adapted to medical applications. Extremely flexible, highly resistant and smooth, its unique features make a real di erence compared to other materials with similar elasticity and robustness. Northwire’s latest innovation may very well change silicone’s leadership.
Compliant to REACH and RoHS2, BioCompatic is a cable newly designed by Northwire’s research and development laboratories. Made of TPR (Thermoplastic rubber), its performance makes this cable a great alternative to silicone for the medical industry.
Just as flexible and soft to the touch as silicone cables, BioCompatic’s jacket material is much more chemical, sterilization, abrasion, cut and crush resistant. For crush testing, Northwire’s engineers have subjected it to extremes that exceed real-world conditions. In order to evaluate its performance in hospitals, a test was designed to simulate a 200 pound medical gurney (wheeled stretcher) device that repeatedly rolled over the cable. The silicone cable failed after less than 9300 cycles, whereas BioCompatic lasted over 186,000 cycles (twenty times more). BioCompatic can be rolled over, pulled or bent with no danger when handled. It also showed resistance equal or superior to silicone for all sterilization types, such as steam and gamma radiation. Its resistance to extreme temperatures has been tested with steam sterilization, preserving physical properties through over 500 autoclave cycles. BioCompatic has also perfectly resisted the most aggressive exposure to hospital-grade disinfectants, retaining 100% of original material performance after 24-hour total immersion in a variety of chemicals including Betadine, alcohols or hydrochloric acid.
The new cable features more than just technical advantages. “Compared to the long and costly curing requirements of silicone, the industrial processes are much shorter and price-competitive at Northwire. It takes 10 to 12 weeks to deliver a silicone solution, whereas BioCompatic is available in 5 to 15 days.”, explains Krista Lindquist, Materials and Manufacturing Engineer.
BioCompatic meets the strictest specifications in its main application field, such as ISO 10993-5 for cytotoxicity, or USP Class VI certification, guaranteeing compliance with United States Pharmacopea (USP) for health care technologies. Containing no halogens, latex or phthalates, it could also become the ideal material for the food industry. Environment friendly, its composition is free from products derived from animal origin.
BioCompatic is the first product launched by Northwire since its acquisition by LEMO in 2014. Fitted with LEMO connectors, it is a perfect example of fully integrated end-to-end solutions that the LEMO Group is now capable of supplying to its customers. Proving LEMO’s strong interest for innovation, this cable was developed in record time, thanks to the Wisconsin company’s expertise and technical network. A 41-year industry veteran, Kevin DePratter, Northwire’s Director of R&D remembers: “We worked around the clock, seven days a week. In four months, the new cable was finished and had obtained all the certifications.”
BioCompatic was officially presented at the 2015 Pacific Design and Manufacturing show, held in February in Anaheim, California. The multi-ways type will be available to the market early spring.